

革の製造工程
― 中山大輔の工場見学 ―

(1)塩蔵北米産牛原皮(ヘビーステア)を塩で腐敗を防いで、銀面を内側にしてたたんでいます。

(2)塩まみれの牛皮をドラムの中で水と一緒にゴロゴロ回し塩抜きします。

(3)まだ毛の付いた状態の塩抜きした牛皮です。背中で半分に割ってなめします。ここまでが準備段階。さあ、本格的ななめしの開始です。
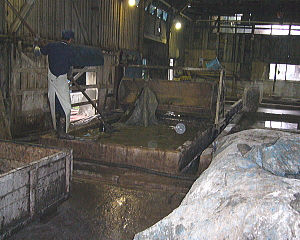
(4)脱毛するための石灰槽での工程です。皮の表面を傷めないように1週間かけて脱毛しているそうです。この写真の前に、パドルという装置に石灰と一緒に皮を入れて回します。強アルカリの中で皮を膨潤させます。この写真はハスペルという装置で、硫酸の中に革を漬けます。酸によって毛を溶かすのと、アルカリを中和します。硫酸の為危険です!
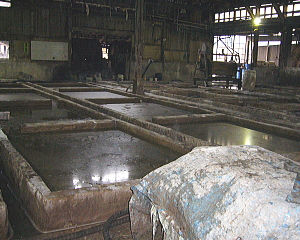
(5)上記石灰槽の写真です。濃度を変えてある為に、漕がいくつもあります。

(6)漕から出された革に付いている余分な脂肪などをフレッシングマシーンで漉いています。

(8)なめすための工程です。漉いた後の皮で、これから漬け込む作業に入ります。
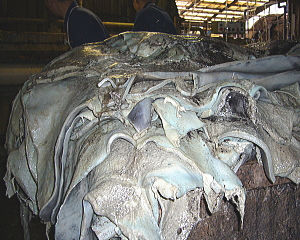
(7)漉く前の皮です。皆さんの手にする革までまだまだ時間がかかります。

(9)渋槽の中で、まんべんなくなめすことが出来るように1枚1枚紐でくくりつけて等間隔で吊り込んでいました。牛革の半裁を65枚ワンピットで漬け込んでいます。
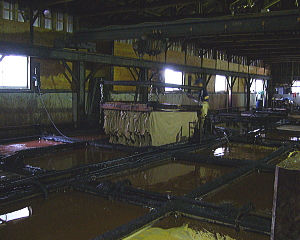
(10)なめすためには最低4つの濃度の違う槽へと移動していました。これがピットという装置で、渋漕に漬け込みます。(俗に言うプールです。)薄い濃度から濃い濃度へ徐々に移動しているそうです。

(ミモザ)アカシアの樹皮より抽出したミモザを使っていました。

(11)ピットの全体図です。植物性のタンニンで、濃い濃度から薄い濃度に漬ける為、これだけのピットがあります。このピットで揺らしながら約一ヶ月漬け込み、皮から革になってい きます。実際見ると写真で見るより圧倒されました。

(12)渋漕から出された革を、水分を抜く為に絞る機械です。


(13、14)ドラムの中で加脂する作業です。風合いを出す為の結構重要な作業なのです。

(15)加脂された革を厚さを均一にする作業です。

(16)仮干しする為に紐をつけています。

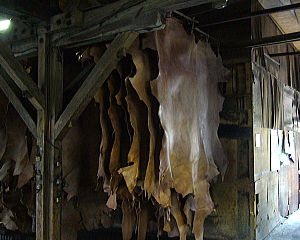
(17,18)一日仮干ししています。どの季節でも同じ室温にするために、ヒーターをつけています。
見学に行った日も軽く汗をかきました。

(19)直射日光が当たらないように風通しのよい場所で約2週間乾燥させています。

(21)色艶を整える為に塗料を吹き付けています。

(20)注文通りの厚さにする為にバンドマシーンで職人さんが漉いています。
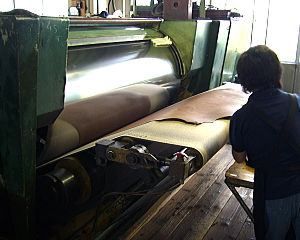
(22)表面を整える為にアイロンをかける作業です。
一生宝物にできるジュエリーとレザークラフト。手作りにこだわりオーダーメイドやカスタムも承ります。